What Is Aluminum Extrusion?
Aluminum extrusion involves heating an aluminum alloy and pushing it into a die with a pre-designed cross-sectional shape. During operation, strong ejector pins push the aluminum through the die and along the dancing table. Often, you can modify the opening of the mold to create a variety of shapes and sizes to meet your product specifications. The process is a simple technique; fundamentally easy to understand. The force used to squeeze aluminum is similar to that used when pressing a tube of toothpaste with your finger. In addition, the extrusion die has a function similar to the opening of a toothpaste tube. Because the opening is a solid circle, the extrusion is a long solid extrusion. There are two main aluminum extrusion technologies – direct extrusion and indirect extrusion.
Direct Aluminum Extrusion
This is the most commonly used extruded aluminum technology. Aluminum extrusion machines place billet/heated aluminum into a container with heated walls while moving punches forcefully push the metal through the die opening. This step creates a lot of stress. Additionally, machinists often place a block of material between the heated aluminum (billet) and the punch to prevent them from touching. Most suppliers and manufacturers call this technology a direct/forward extrusion process because the aluminum and punch move forward in the same direction.
Indirect Aluminum Extrusion
Indirect or reverse extrusion is quite different from direct techniques. During this process, the heated aluminum and container move simultaneously while the mold remains in the same position. Mechanics often use a “rod” to do this. The length of the rod must be longer than the length of the container. Thus, the rod forces the aluminum billet through the stationary die. Reverse extrusion produces less friction than direct extrusion techniques. It has better thermal control. This result may be the result of applying a force, which is relatively constant. Additionally, consistent temperatures ensure better grain structure and mechanical properties. Therefore, the product quality of indirect extrusion is usually reliable.
A Stepwise Guide To The Aluminum Extrusion Process
Step 1: Preparation of the Extrusion Die
The first step involves creating a circular die or using an existing die if available. Before starting the extrusion process, the die is precisely preheated to 450-500ᵒC. This ensures the uniform flow of metal and maximizes the die’s lifespan. Once the die is preheated, it can be loaded into the extrusion machine.
Step 2: Preheating the Aluminum Billets
Next, cylindrical steel billets are cut from stretched logs and preheated in an oven to 400-500ᵒC. This preheating technique prepares the billets for plasticity and manipulation, ensuring they do not melt during the process.
Step 3: Transferring the Billets to the Extrusion Machine
The preheated billets are mechanically transferred to the press. However, before filling the billets into the press, lubricants are added. Additionally, a release agent is applied to the extrusion stem. This helps prevent the billets from sticking to the punch.
At this stage, the forgeable billets are ready in the extrusion machine. Here, the hydraulic cylinder can apply a precise pressure of 15,000 tons. This pressure forces the malleable billet to enter the container, stretching the aluminum material until it fills the container walls.
Step 4: Extruding the Material onto the Die
The aluminum material filling the container walls is pressed onto the extrusion die. Continuous pressure is applied to the material. As a result, the extruded material emerges through the fully formed die opening.
Step 5: Quenching the Extrusion
The puller grips the extrusion and holds it in place as it exits the press. It protects the extrusion while the alloy undergoes a “quenching” process as it moves along the table. The profiles are uniformly cooled using a water bath or fans.
Step 6: Cutting the Extrusion to the Length of the Table
Once the aluminum profiles reach the total length of the table, they are cut using a hot saw. However, it’s important to note that temperature is essential at each step of the extrusion process. Despite the quenching process, the extrusion may not be completely cooled.
Step 7: Cooling the Extrusion to Room Temperature
After the cutting process, the extrusions are moved from the runout table to a cooling area. The profiles remain there until they reach room temperature. Once at room temperature, stretching begins.
Step 8: Transferring the Extrusions to the Stretcher
At this stage, you may notice some distortion in the shape of the extruded aluminum profiles that needs to be corrected. Having a stretcher to straighten the profiles can be helpful. By manually gripping the different ends of each profile and pulling them simultaneously, you can straighten them completely. This process helps adjust the extrusions to the desired specifications.
Step 9: Transferring the Extrusions to the Cut-Off Saw and Cutting Them to Specific Lengths
At this stage, when the extrusions are fully straightened and work-hardened, they can be moved to the saw table. The next step is cutting the extrusions into the desired lengths, typically ranging from 8 to 21 feet. Once the saw cutting process is complete, the extrusions are moved to the aging oven to reach the appropriate temper condition (T6 or T5).
Step 10: Perform secondary operations (heat treatment, fabrication and surface treatment)
After the extrusion process is complete, you can enhance the properties of these profiles with heat treatment. After heat treatment, consider making extrusions if there are dimensional corrections that need to be made. Additionally, adding surface treatments can help enhance the aesthetics and corrosion resistance of extruded aluminum.
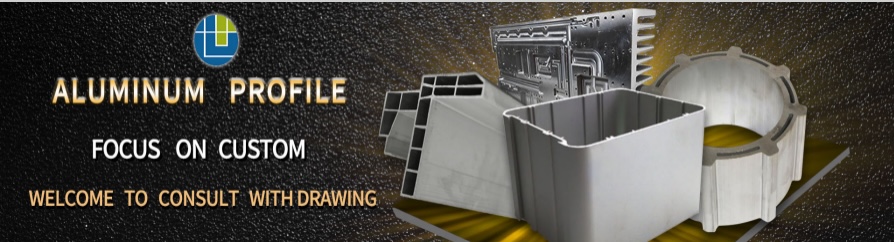